Paper manufacturing consumes a lot of energy, wood and water. Uwe D'Agnone has developed an alternative, which helps protect resources in the sense of a circular economy: his company Creapaper makes paper and cardboard from grass – with resounding success. Large mail order companies already use the product as packaging material.
Uwe D’Agnone kept the piece of paper that started it all. It is quite thick and wavy, and you can see small green specks in it. This sheet of paper, made on a traditional paper sieve, was the first attempt at turning an idea into a new product. It was the first piece of grass paper the businessman made together with a paper maker from Rheinbach. That was eight years ago. It bears no resemblance to today’s paper quality – that’s how much progress Creapaper has made.
“I enjoy setting tasks for myself. I’m a tinkerer,” says the 56-year-old. Uwe D’Agnone trained as an industrial management assistant at an intaglio printing plant with sites in Mönchengladbach and Dusseldorf. In 1990 he started his own business in Hennef, about 20 kilometres from Bonn, Germany His company is called Creapaper, and more than 50 full-time employees now work there. Mr D’Agnone produces advertising materials made of seeds and biodegradable paper for clients like the chemists’ chain DM, the food producer Danone or the Greenpeace environmental protection organisation. For example, the “herb garden”: basil, thyme, cress and Thai basil grow from a simple cardboard box – it doesn’t need to be potted or planted in a garden bed.
In recent years, however, another product, Creapaper’s second mainstay, has moved more and more into the foreground: grass paper. Uwe D’Agnone has set himself the ambitious goal of establishing a more sustainable alternative to paper made from wood.
Not so long ago, people prophesied that paper would disappear. E-books and tablets were taking over the world and buzzwords like “paperless office” were making the rounds. And sure enough, noticeably less paper is being used to print magazines, newspapers and books. Nevertheless, per-capita consumption has been strongly increasing for years. This is primarily due to the enormous boom in online business. All the products purchased in large numbers on the Internet also have to be packaged, of course. These developments are happening quickly: more than ten million packages are shipped every day in Germany. In just two years, the number has more or less doubled. So paper and cardboard will be needed for a long time to come.
But Uwe D’Agnone wasn’t only interested in maintaining the supply of traditional paper. “A few years ago, I read an article about how forest areas as large as Switzerland are cleared every year in countries like Indonesia. My thought was that someone has to do something about this,” he says. The businessman has been working with paper for many years now. So he started experimenting to see what raw materials could be used for manufacture instead of wood – and after a few attempts with diverse fibres, he ended up with grass or, more specifically, hay.
Continue reading below the gallery.
Visionary
Uwe D’Agnone, an entrepreneur from Hennef in North Rhine-Westphalia, wants to shake up the paper market – with grass paper.
First steps: from the testing to real operation
After the initial attempts with the paper maker from Rheinbach, Mr D’Agnone found a paper factory in the Eifel region that was prepared to use one of their machines to test manufacturing paper that was mostly made of grass. The result satisfied the entrepreneur and spurred him on to further experiments. With the Papiertechnischen Stiftung foundation based in Heidenau, Saxony, he tested diverse formulas for his grass paper. Which fibre is suitable for which type of paper? How high can the grass content be? How much wood does it still need to contain? He got in touch with the University of Bonn and set up a partnership with the scientists from the department of renewable raw materials research in the agricultural department. The German Federal Environmental Foundation ( Deutsche Bundesstiftung Umwelt) funded the project. Martin Höller, a young researcher from Bonn, wrote his degree thesis on the development of grass paper.
Hay must first be dried and milled before it can really become paper. Afterwards it is processed into pellets – this also makes it easier to transport. A company from the Münsterland region in Germany used to handle this step for a while, but now Creapaper has put its own pellet production plant into operation in Düren. The hay in pellet form looks similar to animal feed. At the paper factory, the pellets are dissolved in water and can then be processed further. D’Agnone says that his grass paper can probably be used for 90 per cent or more of all typical paper products today. Only transparent paper cannot be produced this way. The share of grass fibres in the cardboard he is currently producing is approximately 50 per cent. The rest is recycled paper or fresh fibre from wood. “But we’re working on increasing the share of grass,” says D’Agnone.
“I have the opportunity to really set something in motion with my grass paper.”
What makes his product the better paper? The entrepreneur claims that “CO2 emissions are approximately 75 per cent lower than for the production of traditional paper”. “The ecological footprint is much better.” Uwe D’Agnone proudly lists the advantages of his grass paper. Only two litres of water are used in the process of manufacturing one metric tonne of his pellets. Producing one tonne of pulp from wood, which is necessary for paper production, takes about 6,000 litres of water. Comparing the energy footprints yields similar results: producing one tonne of wood pulp consumes around 6,000 kilowatts of electricity; the same amount of grass pellets can be made with 137 kilowatts. And chemical additives are not necessary for manufacturing these pellets unlike pulp production from wood. Furthermore, the transport routes are often very long for wood, which is used in the paper factories as processed pulp. In contrast, Uwe D’Agnone produces his pellets as close to the factories as possible. In future, his goal is to process hay for his grass paper within 50 kilometres of the respective factory.
A major contract is helping Creapaper push ahead
D’Agnone sees his company as part of what is known as the circular economy, which strives to produce in such a way that natural materials are not consumed, but preserved. “The main responsibility for turning the corner now lies with the private sector,” he says. “In an industry as powerful as the paper industry, alternatives that conserve resources and are low in emissions are in high demand. With grass fibres in the paper we have found a way to really make a difference. Thanks to this method, we can preserve trees that have a much more important role than just supplying us with wood.” This is what motivates him.
In the beginning it was hard for the entrepreneur to convince paper producers to process his grass pellets. The operators were very worried that the grass could damage their equipment. The cooperation with Otto Versand was what made Mr D’Agnone’s first major contract possible. He was tasked with manufacturing shoe boxes for the mail-order company. With the lucrative order behind him, he was able to win over a paper manufacturer as a partner. Today, a total of 26 paper factories in five countries cooperate with Creapaper throughout Europe. Mr D’Agnone has been working with the Rewe supermarket chain for quite some time. Creapaper manufactures the cartons the group uses to sell its organic apples. But the businessman also wants to expand internationally with his grass paper. He was also able to acquire the beverage manufacturer Coca Cola as a customer some time ago. And he expanded his product range. Creapaper now also makes cups and drinking straws. Toilette paper and paper towels are slated to be added in 2020.
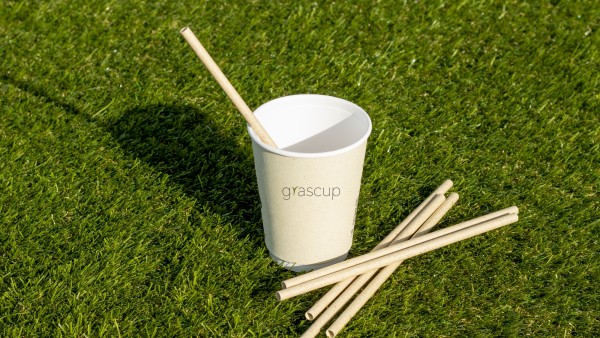
Meanwhile Creapaper also produces drinking straws and cups.
The entrepreneur has received considerable recognition for his project to make paper production more sustainable: for the KfW Entrepreneurs’ Award 2017 corporate competition, Creapaper was first selected as the state winner for North Rhine-Westphalia and subsequently also received the award as the national winner of the KfW Entrepreneurs’ Award 2017 in Berlin. KfW holds a stake in Creapaper via the German venture capital investor eCapital. “The motivation you get from these awards is incredible because you realise that people appreciate what you do,” D’Agnone said at the awards ceremony. Further awards followed: third place in the NRW Start-Up Award 2018, the 2018 Ludwig prize for small and medium-sized businesses in the category of sustainability, and Creapaper was one of seven winners of the German Innovation Prize for Climate and the Environment 2018.
With an eye on growth curves in the area of packaging, Uwe D’Agnone also sees his search for more environmentally friendly alternatives to traditional paper made from wood as his life’s mission. “I have the opportunity to really set something in motion with my grass paper,” he says.
Published on KfW Stories: 13 October 2017, last updated: 2 December 2020.
The described project contributes to the following United Nationsʼ Sustainable Development Goals
Goal 9: Build resilient infrastructure, promote sustainable industrialization and foster innovation
Non-existent or dilapidated infrastructure hinders economic efficiency and thus engenders poverty. When building infrastructure, the focus should be on sustainability, for example, by promoting environmentally-friendly means of transport. Factories and industrial facilities should also ensure that production is in line with ecological aspects to avoid unnecessary environmental pollution.
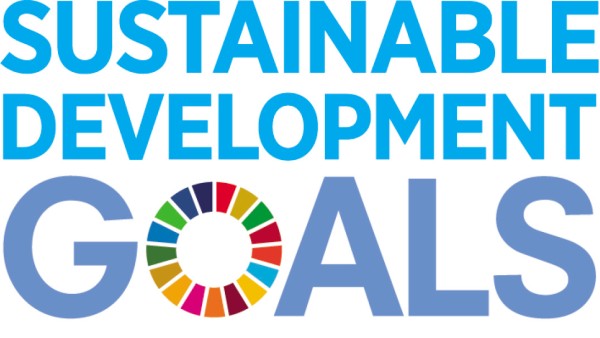
All United Nations member states adopted the 2030 Agenda in 2015. At its heart is a list of 17 goals for sustainable development, known as the Sustainable Development Goals (SDGs). Our world should become a place where people are able to live in peace with each other in ways that are ecologically compatible, socially just, and economically effective.
Data protection principles
If you click on one of the following icons, your data will be sent to the corresponding social network.
Privacy information