Doesn’t lightweight furniture buckle under pressure? Not at all! An engineer in the Bavarian town of Bad Aibling has invented a wooden composite made of sustainable raw materials, which is especially lightweight and durable at the same time. And since there were no machines out on the mass market to suit his innovative idea, with his company "Lightweight Solutions" he also developed the production lines for his own product.
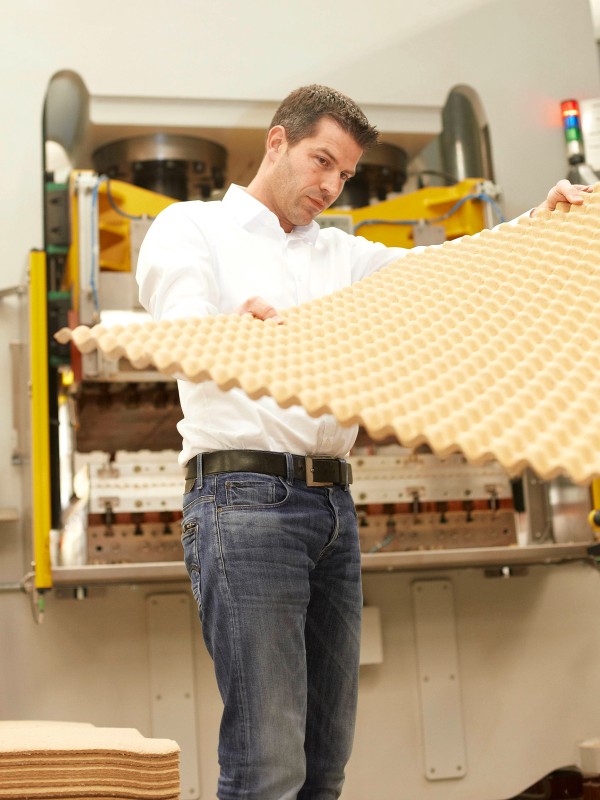
The lisocore lightweight panels are made from light, but solid and recyclable natural fibres.
It all started with an old T-shirt. Michael Schäpers soaked the material in resin, alternately pressing in balls from above and below and sticking the undulating structure he had fashioned between two panels. His creation was lightweight, while also being stable and resilient. “I showed my professor the results, and he advised me to get my idea patented as soon as possible,” the engineer recalls, adding: “Initially, I could hardly believe that this wasn’t already out there.” The idea came to him in a statics lecture at Rosenheim University of Applied Sciences, where he was studying Wood Technology as a 27-year-old. Eight weeks later, the patent application for an innovative building material was filed, and the skilled carpenter became a start-up entrepreneur – all while still being a student.
In fact, Michael Schäpers had not at all been planning to build his own business. “But what else was I supposed to do with my idea?” he asks, his previously serious expression making way for laughter-lines. Today, the 40-year-old manufactures lightweight construction panels branded as lisocore, which are made from natural fibres, weigh little, and are highly stable and recyclable. He hopes that these provide the market with a sustainable alternative to conventional wooden composites. The material is assembled according to the sandwich principle: a three-dimensional, wave-shaped core structure is wedged between two layers of wood. The whole thing looks like a carton of eggs stuck between two boards.
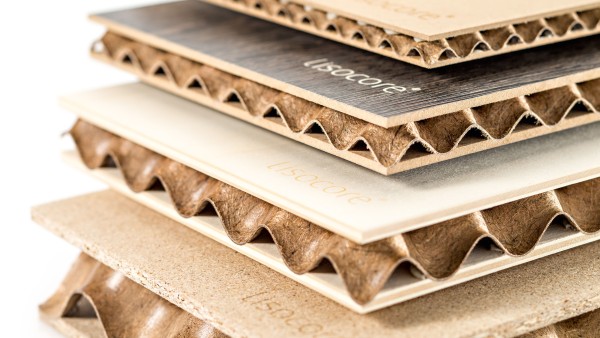
Large production lines were needed to mass-produce the lightweight construction material.
When he founded Lightweight Solutions in March 2004, there was a room free in his student flatshare. Michael Schäpers made it into his first office. The first member of staff, a fellow student, still works for him to this day. “Back then, we thought about how you could produce the wooden composite and would always hit a stumbling block,” Schäpers remembers. “We needed material, methods, technology and machines. And since we had obviously come up with an innovation, all that wasn’t available.” The two wood technology engineers heard from big-name machine manufacturers that the project would not be feasible to implement. But that did not discourage them. To the contrary, says Schäpers: “From that point of adversity, we started to build our machines ourselves.” Thus the first small press was created, along with key processes to develop the production of lisocore. More than a year later, the company moved to a proper office in nearby Stephanskirchen. Soon after, their numbers swelled to seven, with most of the staff also studying in Rosenheim.
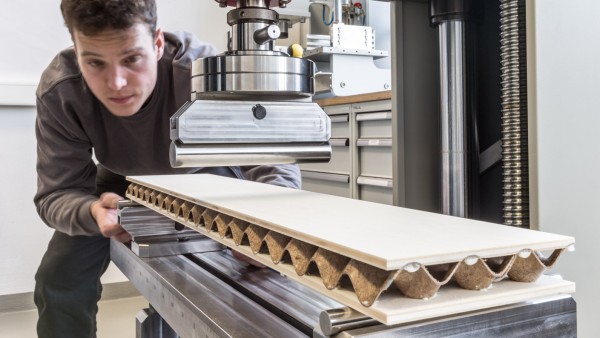
The company received support from the KfW Environmental Innovation Programme, from the Federal Ministry for the Environment, Nature Conservation, Building and Nuclear Safety, as well as from the Federal Environment Agency, so that the environmentally-friendly procedures could be used for the first time in Germany.
Lightweight Solutions won the Schweighofer Innovation Prize with lisocore in 2009. This is akin to a Nobel Prize in the wood industry. It was a turning point for Michael Schäpers. “This made big names in the industry aware of us,” he recounts. One example was Walter Schatt, a well-known decor printing entrepreneur in the region. Schäpers’ situation reminded Schatt of his own time as a start-up founder. After many discussions, he joined the company as its second equity holder “He had the forward-looking approach that was necessary, he had a large number of contacts and he’s an important mentor to me,” Schäpers says of the experienced businessman.
Large production lines were needed to mass-produce the lightweight construction material. However, this equipment costs millions of euros. “We put a lot of thought into the location and developed an environmental master plan,” Schäpers explains. To this end, he received a commitment from the Environmental Innovation Programme of KfW, and Germany’s Environment Agency and Federal Ministry for the Environment, Nature Conservation, Building and Nuclear Safety.. This programme supports environmentally-sound processes adopted in Germany for the first time. In total, Lightweight Solutions received around EUR 2.3 million in support between 2010 and 2015.
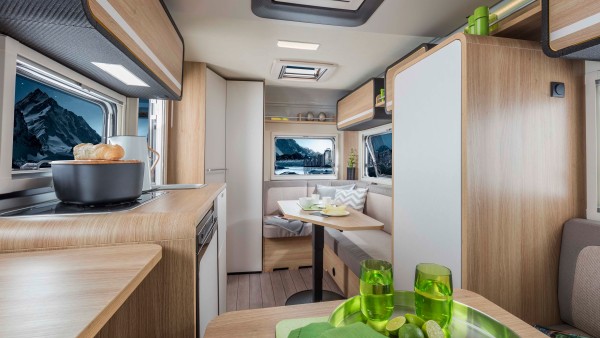
The lightweight design provides many advantages in the automotive industry as well. For example, their light weight ensures a reduction in CO2 emissions when driving.
“This gave us the opportunity to build a completely new technology in a prudent way,” Schäpers states. The company moved to the industrial estate in Bad Aibling in 2010, occupying a former US military barracks. Within five years, the engineer and his workforce – by that point numbering 26 staff – developed and assembled a large-scale industrial facility for lisocore. “The company did not manage to construct the innovative production facility and commence operations on its own within the planned time-frame,” recalls KfW’s Matthias von Zedlitz, who works in the team responsible for the Environmental Innovation Programme at the promotional bank. He adds: “The project is a model example of how an environmentally-friendly product can be manufactured while simultaneously reducing human impact and achieving financial viability.”
For Schäpers, the founder, it was a time filled with strenuous effort. “We couldn’t know whether the machine would run until the last moment. If it didn’t, that would have been the end of the company without a doubt,” he remembers. But when the first lisocore panel rolled through the new production line in 2015, it was just the beginning. “We have only been able to enjoy any sort of proper production since that point – our prototype machine previously had no capacity,” Michael Schäpers points out. With an output of two million square metres of panelling, the system now drills 18,000 holes in under 15 seconds, at the same time shooting a bead of adhesive into each hole. “And the machine runs like a dream!” the inventor is visibly proud to add. Energy consumption is also optimised for efficiency within production via recirculated waste heat from the process and use of variable hydraulic drives.
As the managing director leads the way through the production plant and testing laboratory, with the sounds of local radio station Bayern 3 playing in the background, he enthusiastically speaks of gap dimensions, servomotors and other technical details. Even if the uninitiated might not understand much about it, one thing is clear: What he has achieved with lightweight solutions in Bad Aibling is true engineering artwork.
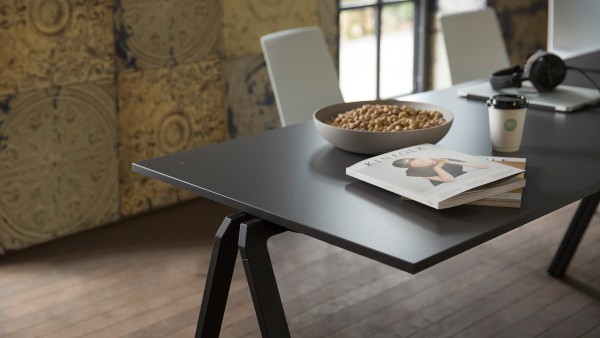
Together with a furniture maker, lightweight solutions developed a slender, but highly resilient tabletop, for which it received international design awards.
However, the product has been difficult for the market to accept, according to Schäpers. “Many people in the wood industry consider lightweight material tacky,” he explains: “But they are making a big mistake. Lightweight construction is a top-tier discipline in the automotive, aviation and aerospace industries.” He wishes to make it plain to his customers that the lightweight design provides other advantages aside from its low weight. For example, he partnered with a furniture maker to develop a slender and highly resilient tabletop, with the table going on to win an international design award. In addition, the company invented a height-adjustable, sit-to-stand table together with another manufacturer, which also won prizes. All its technical equipment, such as its wires, motor and control unit, were concealed inside the wooden top’s cavities. lightweight solutions took on the job of providing the entire set of interior fixtures and fittings for a series of caravans. Their light weight will ensure a reduction in CO₂ emissions while on the road.
Source

More information about other innovative companies in the spring/summer 2018 issue of CHANCEN magazine focusing on “Innovation”.
To German editionAside from the core structure for the Lisocore lightweight construction panels, the production lines can also be used to manufacture compression-moulded parts; for instance, for packaging used in logistics or upholstery padding for chairs. Michael Schäpers has built up a second source of income with this. And he is currently patenting another idea: “In the future, we also want to make the core structure ourselves,” he reports.
Michael Schäpers is not yet sure whether the winds of the future will blow in the direction of mass production or niche product manufacturing. There is enough space for more production systems in Bad Aibling. The company has close to 100,000 square metres of space into which to expand. Construction plans have been drawn up. But the business founder strikes a humble tone: “Now we have to get through the market entry phase – everything else will reveal itself in the years to come.”
Followed up on 13 November 2020
In 2020, Lightweight Solutions GmbH became Pyrus Panel GmbH and is now a 100% subsidiary of RETIS Holding GmbH. The new managing director is Robert Vuga. The innovative construction material lisocore remains in the focus, it has won the Green Product Award in 2020 and is among the finalists of the German Sustainability Award 2021.
A piece of furniture made of Pyrus Panel GmbH's lightweight panels is likely to become part of many European dining rooms in 2021. IKEA has added the "Tranebo" table to its product range. In Sweden, it is already available.
Published on KfW Stories on 28 August 2018, updated on 13 November 2020.
The described project contributes to the following United Nationsʼ Sustainable Development Goals
Goal 9: Build resilient infrastructure, promote sustainable industrialization and foster innovation
Non-existent or dilapidated infrastructure hinders economic efficiency and thus engenders poverty. When building infrastructure, the focus should be on sustainability, for example, by promoting environmentally-friendly means of transport. Factories and industrial facilities should also ensure that production is in line with ecological aspects to avoid unnecessary environmental pollution.
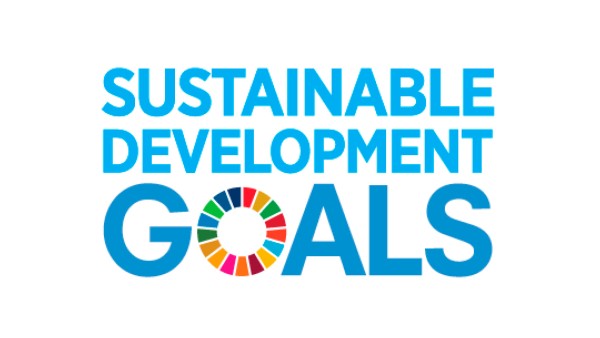
All United Nations member states adopted the 2030 Agenda in 2015. At its heart is a list of 17 goals for sustainable development, known as the Sustainable Development Goals (SDGs). Our world should become a place where people are able to live in peace with each other in ways that are ecologically compatible, socially just, and economically effective.
Data protection principles
If you click on one of the following icons, your data will be sent to the corresponding social network.
Privacy information