In the middle of extensive Hessian beech forests, Furnier- und Holzwerk Mittenaar GmbH has been producing beech peeled veneers for over 50 years. Demand is greater than ever at the moment. A good time for the mid-sized company to invest in energy efficiency and energy security. A highly efficient biomass plant to supply heat was commissioned for around 6.7 million euros.
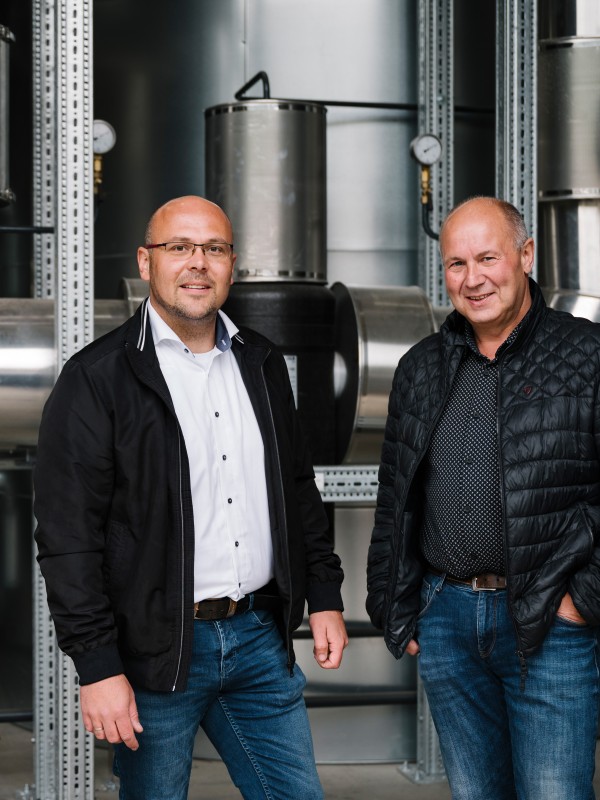
Furnier- und Holzwerk Mittenaar
From left: Martin Bettner, Head of Energy Projects at the Weimer Group, and Hartmut Dietermann, Managing Director of Furnier- und Holzwerk Mittenaar.
Hartmut Dietermann has experienced many turbulent times in the timber trade. “But it has never been like this before,” marvels the Managing Director of Furnier- und Holzwerk Mittenaar GmbH in the Hessian district of Lahn-Dill. The huge peeling machine never stops turning in the background as he talks about the unrelenting demand for beech peeled veneers and firewood. Layer by layer, it cuts almost endless veneer sheets out of the beech trunks. Just a few steps away, the veneer sheets go through an elongated drying line, where they are dried and flattened like in an oversized iron. The employees routinely remove undesirable irregularities in the wood – a kind of continuous quality control before the dried veneers are optimally cut to customer requirements at the end of the 70-metre-long production hall.
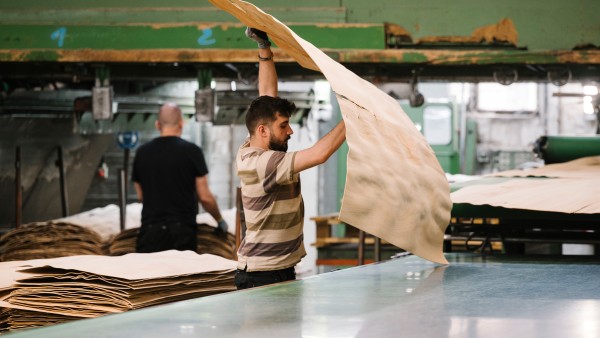
Three-shift operation
The employees routinely remove unwanted irregularities in the wood growth.
“Our production is carried out in a three-shift operation,” explains Dietermann, returning to the conversation about the extraordinary times: On the one hand, climate change has affected things. It is having a negative effect on the forests in these parts and many trees suffer from drought and pest infestation. Even though beech trees are actually resilient, the water shortage is an additional stress factor. At the same time, the global construction boom has caused an explosive demand for wood. Then the coronavirus pandemic destabilised global supply chains in the timber business, and we are now losing two of the world’s largest timber suppliers, Russia and Ukraine.
Unsettled times are nothing new to the team in Mittenaar. Wood has been processed in the district of Bicken for around 150 years. Veneered wood production started at the site more than 50 years ago. Then in 2014, it looked as though the tradition was coming to an abrupt end. As the company was sliding into insolvency, Hartmut Dietermann, who had been operations manager for a long time, was no longer part of the team. But he returned and has experienced a remarkable turnaround since 2018. The diverse Weimer Group from Lahnau in cooperation with Kreiling Beteiligungs GmbH based in Gießen took over the veneer plant and since then all the signs indicate modernisation and growth.
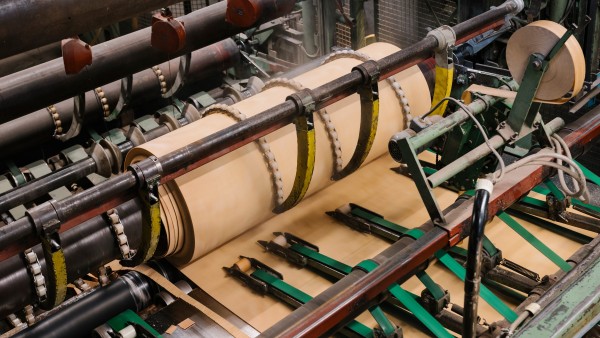
Quality control
The veneer webs pass through a long stretched dryer line.
There is great demand for peeled veneers – with a manageable number of competitors. This creates a special market structure: “We all have our own areas of specialisation, serving our own niche markets,” Dietermann describes the industry. The niche of the Middle Hesse company is industry, and transformer construction in particular. Veneers are used as an insulation material in this field. “Copper beech wood is non-conductive and has the best electrical properties for use in transformers,” explains Dietermann on the benefits of his veneers. And transformers are needed “also for the development of renewable energies.” The company supplies a small part of its production to the furniture industry. Firewood is made out of the leftover wood from veneer production – demand for it has risen dramatically as well.
Something else the experienced wood specialist has never experienced like this before in his long career at the veneer plant: “Since the acquisition, the Weimer Group has invested heavily in the restructuring of the company.” Some of the systems built on the veneer plant’s premises over fifty years ago are now more of a hindrance to efficient production processes. There is not enough space to expand either. With a comprehensive action plan, the veneer production in Mittenaar is now to be redesigned to become more modern, sustainable and energy-optimised. The administration rooms have already been renovated, old buildings had to be removed to create a new wet wood yard and to renew the steam pits.
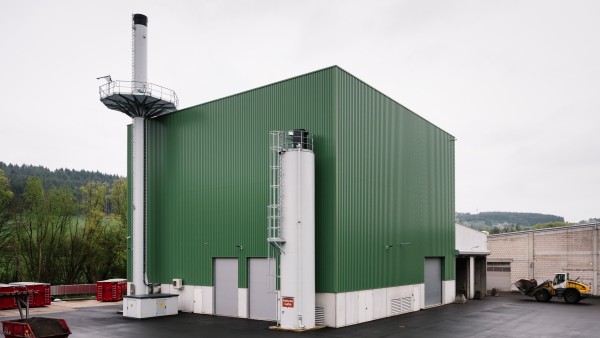
Biomass heating plant
With the highly efficient energy production, CO2 emissions are reduced by 200 tonnes per year, thus making a contribution to climate protection.
2021 saw the end of the old boiler house from the 1960s. It has been replaced by a modern biomass heating plant for the company’s heat supply. “Without a doubt, this is a key investment,” says Managing Director Dietermann. The company invested around 6.7 million euros in the biomass plant between 2019 and 2021.
For Martin Bettner, Head of Energy Projects at the Weimer Group, the investment opens up a whole new dimension of energy efficiency and pollutant reduction in the veneer plant: “With an efficiency level of 90 per cent and a nominal heat output of 8 MW, we can now provide heat for different processes in veneer production.” The high degree of efficiency is made possible thanks to the installation of a second exhaust gas heat exchanger, which once again cools the temperatures from the combustion process to just under 100 degrees Celsius.
This means that different temperature levels can be used in the heat supply for the steam pits, for drying the veneers and the firewood, and for heating the hall. In addition, the system also meets all air pollution control requirements thanks to complex exhaust cleaning at a new location which is further away from residential buildings. “With the biomass plant, we are reducing our CO2emissions by 200 tonnes per year,” says Bettner, quantifying the contribution of the veneer plant’s highly efficient energy generation to climate action.
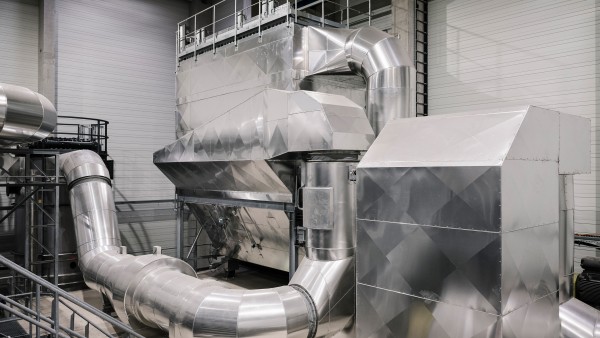
Biofuel
The plant is fired with waste wood and residual wood from production.
The plant is fired with waste wood and leftover wood from the production. When processing around 18,000 solid cubic metres of peeled wood and 10,000 solid cubic metres of firewood every year, sufficient biofuel is naturally produced. Fossil fuels, on the other hand, are not used for heat generation in the company. In the face of global fossil energy crises, the Hessian company is truly ahead of the times. From raw materials for production to biofuel for the heat supply, the company operates strictly regionally, and almost entirely utilises the raw material wood.
Due to the high energy efficiency and the use of well over 50 per cent of the heat generated for the production process, the mid-sized company was able to take advantage of federal funding for energy efficiency in commerce, a low-interest, large-volume promotional programme with high repayment bonuses from funds from the Federal Ministry for Economic Affairs and Climate Action. “Of course, the maximum repayment bonus of 55 per cent for our biomass plant was a decisive factor in being able to tackle an investment on this scale,” says Hartmut Dietermann.
However, his focus is already on further modernisation plans for the future. But the construction cranes that are currently on the company premises are not part of these plans. They belong to the central fire station that the local authority is planning to build on the company premises. Also a sign of how firmly anchored the established enterprise is in Mittenaar – as firmly rooted as the beech trees in the Hessian forests while embracing the energy-efficient production of tomorrow at the same time.
The plant is fired with waste wood and leftover wood from the production. When processing around 18,000 solid cubic metres of peeled wood and 10,000 solid cubic metres of firewood every year, sufficient biofuel is naturally produced. Fossil fuels, on the other hand, are not used for heat generation in the company. In the face of global fossil energy crises, the Hessian company is truly ahead of the times. From raw materials for production to biofuel for the heat supply, the company operates strictly regionally, and almost entirely utilises the raw material wood.
Due to the high energy efficiency and the use of well over 50 per cent of the heat generated for the production process, the mid-sized company was able to take advantage of federal funding for energy efficiency in commerce, a low-interest, large-volume promotional programme with high repayment bonuses from funds from the Federal Ministry for Economic Affairs and Energy. “Of course, the maximum repayment bonus of 55 per cent for our biomass plant was a decisive factor in being able to tackle an investment on this scale,” says Hartmut Dietermann.
However, his focus is already on further modernisation plans for the future. But the construction cranes that are currently on the company premises are not part of these plans. They belong to the central fire station that the local authority is planning to build on the company premises. Also a sign of how firmly anchored the established enterprise is in Mittenaar – as firmly rooted as the beech trees in the Hessian forests while embracing the energy-efficient production of tomorrow at the same time.
Published on KfW Stories on 20. May 2022.
Goal 9: Build resilient infrastructure, promote sustainable industrialization and foster innovation
Non-existent or dilapidated infrastructure hinders economic efficiency and thus engenders poverty. When building infrastructure, the focus should be on sustainability, for example, by promoting environmentally-friendly means of transport. Factories and industrial facilities should also ensure that production is in line with ecological aspects to avoid unnecessary environmental pollution.
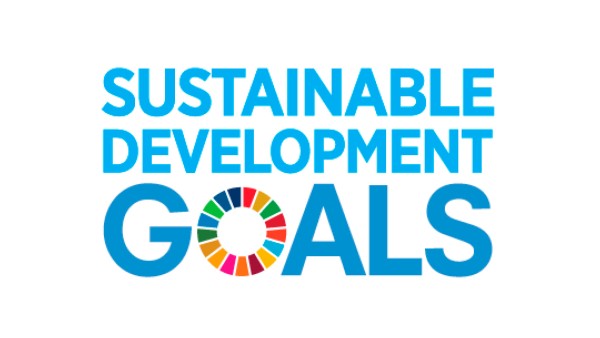
All United Nations member states adopted the 2030 Agenda in 2015. At its heart is a list of 17 goals for sustainable development, known as the Sustainable Development Goals (SDGs). Our world should become a place where people are able to live in peace with each other in ways that are ecologically compatible, socially just, and economically effective.
Data protection principles
If you click on one of the following icons, your data will be sent to the corresponding social network.
Privacy information