If production equipment fails, specialists often need to travel to repair the faults in person. Oculavis has developed a digital solution: its software platform and augmented reality applications make it quick and easy to share information and access visual support. For this work, the start-up was honoured with the KfW Entrepreneurs’ Award as the state winner for North Rhine-Westphalia and winner of the “People’s Choice” award.
Installing a transformer, changing brake pads, setting up a computer – for some mundane but unfamiliar tasks, we need help from experts who can provide us with one-to-one problem-solving support.
Mechanical and plant engineers also encounter many challenges where they need professional help. If, for example, a robot or a CNC milling machine won’t work because the operator cannot identify the underlying problem, it can put the whole production line at risk. That is hugely costly. Furthermore, it can take days for experts to arrive on site. Aachen-based company Oculavis promises fast assistance to help companies and individuals resolve these kinds of challenges themselves.
Managing Director Martin Plutz explains how the remote support module works on the software the company has developed, “No-one needs to stand next to the machine, frantically calling someone and trying to explain the situation. The person using our software grabs a smartphone, tablet or smart glasses, holds the camera up to the equipment and connects to a professional. They can be anywhere in the world. The professional can use augmented reality layers to, for example, draw arrows directly onto the image on the end device or give instructions about components, letting them explain exactly what the next steps are.”
Read more under the image gallery.
The three founders, Martin Plutz, Philipp Siebenkotten and Dr Markus Große Böckmann (f.l.t.r.), are mechanical engineers and computer scientists. This background ensures that they really understand their customers.
Smart glasses as a driver of innovation
Martin Plutz, Dr. Markus Große Böckmann and Philipp Siebenkotten have known each other since their days as mechanical engineering students. Their product Oculavis SHARE came out of the emerging interest in smart glasses. These seemed like the perfect tool for expanding the visually perceived environment in order to provide remote help in real time. The trio started developing software prototypes that made use of these opportunities –and they immediately licensed a version to Bosch. “That showed us that it wasn’t just a crazy idea and that there was actually a market for it. Starting a company was the logical next step,” recalls Martin Plutz.
The team successfully applied for the EXIST grant, which supports start-ups in the sciences. The Fraunhofer Institute and RWTH Aachen business incubator offered the perfect conditions to drive the project forward. This offered the chance to not only use the infrastructure, but also to get students involved. The new company had a staff of ten from the word go. “We got off to a flying start!” jokes Plutz.
Smart test run
Oculavis GmbH was established in May 2016, supported by KfW via a StartGeld start-up loan. An EU grant worth around 2.5 million euros made it possible to professionalise fast. To this day, no external investors have come on board. The company started turning a profit from its first year.
A tour of Germany provided income initially. In cooperation with the Fraunhofer Institute, the start-up offered one-day seminars for companies called "Smart Glasses Experience Days". Here, they introduced the ways these new types of smart glasses could be used, with their software as an example. This gave rise to their first customer relationships.
Oculavis didn’t just concentrate on smart glasses however, not least because they have not been adopted as widely as was originally predicted. Their software is also suitable for use with all standard tablets and smartphones.
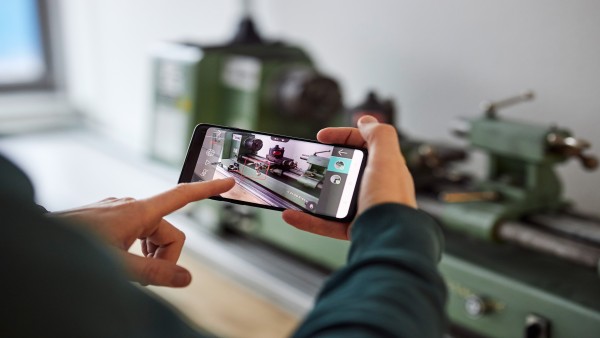
With the digital solution, customers around the world can maintain or repair machines and equipment themselves. A smartphone is used to communicate in these cases.
Use in practice
The "virtual x-ray viewer" is technically complex but extremely user friendly. After scanning a QR code on the equipment in question, in-built content opens, such as step-by-step instructions for maintenance or troubleshooting of standard errors. If the user cannot resolve the problem, the embedded video call function connects to an expert and the Augmented Reality Viewer starts up. Transmission and image quality are guaranteed even when the internet connection is bad. The ISO 27001 certification guarantees that all data is protected.
Oculavis has two target customer groups: machine manufacturers who want to use the Augmented Reality Service tool to offer their customers an additional service, and companies who use it internally. This lets their own technical staff conduct equipment maintenance fully remotely. Customers are granted a licence, meaning that they also benefit from updates. White label solutions ensure that the software can be adapted to their own design.
Servicing and work undergoing transformation
The coronavirus pandemic demonstrates that remote support solutions are vital, as it has been necessary to switch to digital offerings. Martin Plutz also talks of a "clear push".
Oculavis can also help with other changes. Plane journeys to repair automated equipment in Singapore or milling machines in Brazil are no longer necessary. That helps to protect the environment. Furthermore, many people no longer want to do this work, as Plutz explains, "It’s difficult to find young people who want to become service technicians, to motivate them and retain them in the profession. It involves a lot of travel and often that isn’t to the world’s attractive metropolises. Who wants to spend their days in a small town in – let’s say China – mending machines with a stressed customer, and spend their evening sitting in a cheap hotel?" With digital tools, it is possible to do this job while working from home.
In a short space of time, the entrepreneurs and their 60-strong team created an offering that can transform an entire sector. There is a lot of interest, including from the media. This is not only due to the KfW award, but also to the many other prizes that were awarded.
Martin Plutz looks to the future with optimism, "Naturally, there are competitors. But our advantage comes not only from the product’s many good features, but also from our background. As mechanical engineers, we have an in-depth understanding of our customers’ needs and processes, which we can reflect perfectly in the software. We already have 20 partners worldwide who distribute our solutions, and it is our mission to scale up globally."
Published on KfW Stories: 5 February 2021.
Data protection principles
If you click on one of the following icons, your data will be sent to the corresponding social network.
Privacy information